Nitrosys
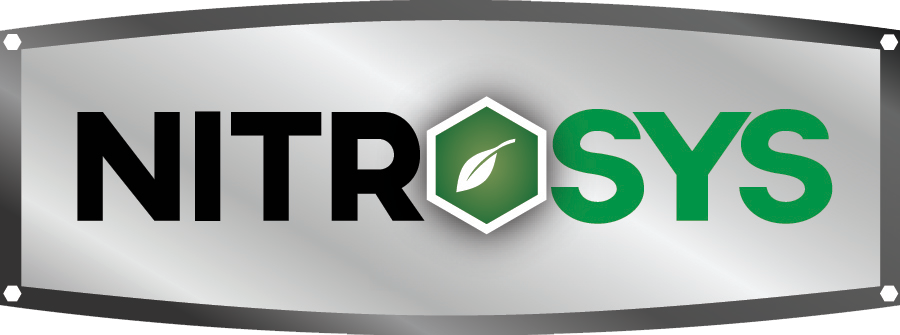
Nitrosys low pressure plural component proportioners heat your materials, meters the materials by volume, and maintains the materials’ heat until it is sprayed or injected.
Why use low pressure?
Because of the characteristics of low pressure SPF, there are many areas where applying low pressure applications has many benefits over applying high pressure applications. Some of these benefits include:
- Faster re-entry time for Nitrosys Refill.
- Reduction of up to 80% in over spray.
- Simple & Flexible Installation
- Reduced noise and power consumption.
- Less equipment required
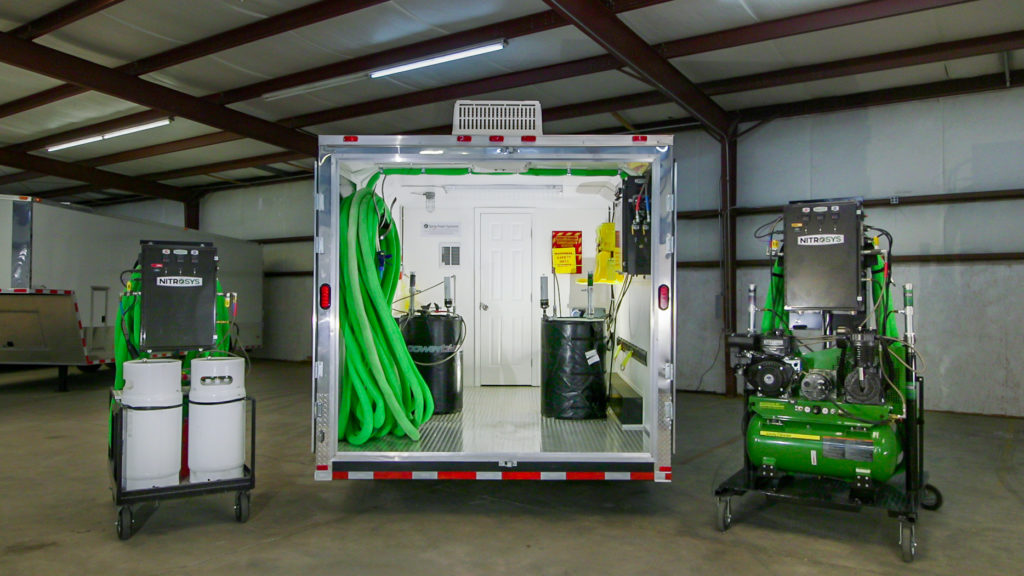
Faster Re-Entry Times
Because of the low pressure static mix that occurs during the application of Low pressure materials, atomization does not occur and VOC’s do not saturate the air; like they do during the application using high pressure systems. For the Nitrosys Refill System, this allows occupants to re-enter the structure only one hour after the spray application has occurred. Also due to the low pressure static mix and no atomization, installers can wear PPE (personal protective equipment) that consists of organic vapor acid gas respirator cartridges. No fresh air pump is required like during the application of High pressure spray foam.
Simple & Flexible Installation
The NiTROSYS Spray Foam System’s preheating, and auto-calibration unit can easily be configured as a mobile cart or skid, in a mobile spray rig or added to an existing mobile spray rig. The spray foam system requires less spray foam equipment to be used and it’s small, compact size allows the unit to be put onto mobile carts, skids, or into smaller vehicles such as a sprinter van.
Reduced Noise & Power
No more extremely loud, diesel, spray foam generators when working with the NiTROSYS Spray System. Less power is required to run the spray system, allowing the applicator to use a much smaller generator or shore power, and reduce the noise produced.
Lower Pressure and Temperatures
Low pressure spray foam application will allow for a reduction of up to 80% in over spray during the application process compared to high pressure spray applications. The process temperature is also lower than high pressure formulations which makes applying low pressure spray formulations in colder climates ideal.